Tanaka Laser Cutting Technology combines high precision, advanced lasers, and efficient material use. Our exploration will highlight the fundamentals, the range of machines Tanaka offers, and how they integrate advanced technologies to improve performance and cutting quality.
Fundamentals of Laser Cutting
Laser cutting uses a focused beam of light to cut materials. This concentrated energy cuts through materials with high precision. Lasers, like CO2 or fiber lasers, vary in application.
Tanaka uses oscillators to control the laser’s intensity, affecting cutting speed and precision. We see a balance between performance and material waste, essential for high-quality outputs.
Tanaka’s Range of Laser Cutting Machines
Tanaka offers a variety of machines tailored to different needs:
- CO2 Laser Cutting Machines: Suitable for thicker materials.
- Gantry CO2 Laser Cutting Machines: Ideal for large-scale projects.
- Gantry Fiber Laser Cutting Machines: Known for high speed and efficiency.
Gantry machines provide robust performance and precise control. They are versatile, handling diverse cutting tasks with ease. We focus on precision and cutting quality to meet various demands.
Integration of Advanced Technologies
Tanaka incorporates advanced technologies to enhance cutting effectiveness. LMRV technology, for example, optimizes laser control, leading to better cuts and less waste.
Automation in Tanaka’s machines allows for continuous operation, improving efficiency. The integration of sensors ensures real-time adjustments and maintains cutting speed and quality.
Advanced software aids in design and precision, aligning with our goal to maximize efficiency. We are strongly committed to using technology for superior performance and reduced material usage.
Design and Material Preparation Strategies

To maximize efficiency with the Tanaka Laser Cutting Machine, we focus on two main areas: optimal material use in cutting designs and precision in material handling.
Optimal Material Use in Cutting Designs
Maximizing material efficiency starts with design. We use Computer-Aided Design (CAD) software to create precise outlines that minimize waste. Nesting techniques, where smaller parts fit within the gaps of larger ones, help reduce scrap.
Using thinner materials can also result in less material removal. However, it’s important to balance this with the strength needs of the final product. Recycling and using recycled plastics in designs can further reduce waste.
To achieve the best results, we analyze the cutting paths in Computer-Aided Manufacturing (CAM) software. This helps us decide the most efficient routes, saving both materials and time. By refining these designs, we can cut costs and improve sustainability.
Implementing Precision in Material Handling
Handling materials with precision ensures reduced waste. We store materials correctly to prevent damage and contamination. Proper storage techniques include keeping sensitive materials away from moisture and direct sunlight.
When setting up the machine, micro connections between parts can be used. These small connections hold the parts together during cutting, preventing them from shifting. This technique avoids the need for additional material to secure parts in place, reducing waste.
Additionally, meticulous setup and calibration of the Tanaka Laser Cutting Machine are crucial. Ensuring the machine is perfectly aligned and its settings are correct prevents errors and material loss. By focusing on precision in every step, from storage to cutting, we reduce unnecessary waste.
Enhancing Efficiency and Sustainability
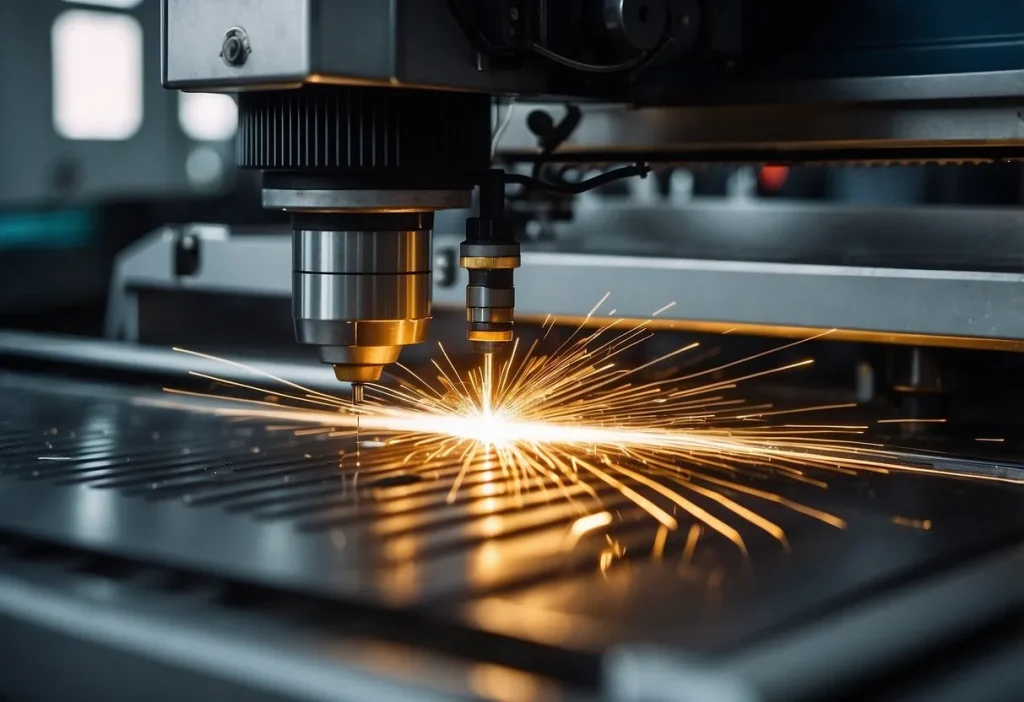
We can improve both efficiency and sustainability by focusing on energy and resource-saving techniques and using sustainable manufacturing practices with Tanaka machines.
Energy and Resource Efficiency Techniques
Using energy-efficient techniques reduces costs and minimizes environmental impact. Tanaka laser cutting machines have optimized cutting times, which lowers energy consumption.
We can also use recyclable materials to reduce waste. Additive manufacturing techniques help us use only the necessary amount of metal, avoiding excess. This method is valuable in industries aiming to increase resource efficiency while maintaining high cutting-performance.
Another useful method is reducing the use of auxiliary gas. We can achieve this by fine-tuning the machine settings, ensuring precise cuts without unnecessary gas consumption.
Sustainable Manufacturing with Tanaka Machines
Sustainable manufacturing involves using resources in a way that minimizes environmental harm. Tanaka machines are designed to be both energy-efficient and capable of recycling materials.
These machines help us reduce the environmental impact by not only using less energy but also incorporating recycling processes. This innovative approach makes them suitable for various industries focused on sustainability.
Implementing these machines in our manufacturing processes ensures we meet industry standards for environmental responsibility while maintaining high productivity. Ensuring both efficiency and sustainability translates into a better future for our operations and the environment.
Operational Excellence in Laser Cutting
Achieving operational excellence in laser cutting involves fine-tuning cutting parameters and conducting regular maintenance and performance checks. This ensures high precision and efficiency in processing metals like steel plates.
Optimizing Cutting Parameters
We must carefully adjust the cutting speed and other parameters to improve precision. For example, different metals have varying melting points which impact their performance.
- Cutting Speed: Higher speeds reduce processing time but may affect accuracy.
- Melting Point: Understanding each metal’s melting point helps in setting the right parameters.
By fine-tuning these factors, we minimize material waste and improve the quality of cuts.
Maintenance and Performance Checks
Regular maintenance keeps the laser-cutting machine in top shape. We check the machine’s components to prevent wear and tear.
- Routine Inspections: Regularly inspect the laser head and lenses.
- Performance Metrics: Monitor performance to ensure consistent precision.
These checks ensure that our machine operates efficiently, reducing downtime and enhancing production quality. Proper maintenance extends the machine’s life and ensures excellent cutting outcomes.
Innovation and the Future of Laser Processing
Emerging technologies like artificial intelligence and the exploration of new laser manufacturing methods are shaping the future. These advancements promise to enhance precision and efficiency.
The Role of Artificial Intelligence
Artificial intelligence (AI) plays a significant role in improving laser processing techniques. AI algorithms help optimize cutting paths, which reduces material waste. By using AI, we can analyze large datasets and improve the accuracy of the cuts.
FMRIii technologies integrated with AI allow for real-time adjustments. This capability means that errors can be corrected instantly, improving the final product quality. AI can also predict when machines need maintenance, reducing downtime.
The interface between AI and laser systems is becoming more user-friendly. This ease of use means that even operators with limited technical knowledge can achieve professional results. AI thus bridges the gap between complex technology and practical application.
Exploring the Frontiers of Laser Manufacturing
Advances in laser technologies are pushing the boundaries of what is possible in manufacturing. These cutting-edge methods include more precise laser beams and new materials. Innovations like FMRIii are leading to faster and more accurate results.
We are also exploring hybrid laser systems. Combining different lasers in one machine allows for a variety of cuts and processes in a single pass. This versatility enhances efficiency and material use.
Furthermore, the integration of lasers with other technologies, such as robotics, opens new possibilities. Robots equipped with laser cutters can work around the clock and execute intricate designs. This development not only boosts productivity but also maintains high standards of precision.